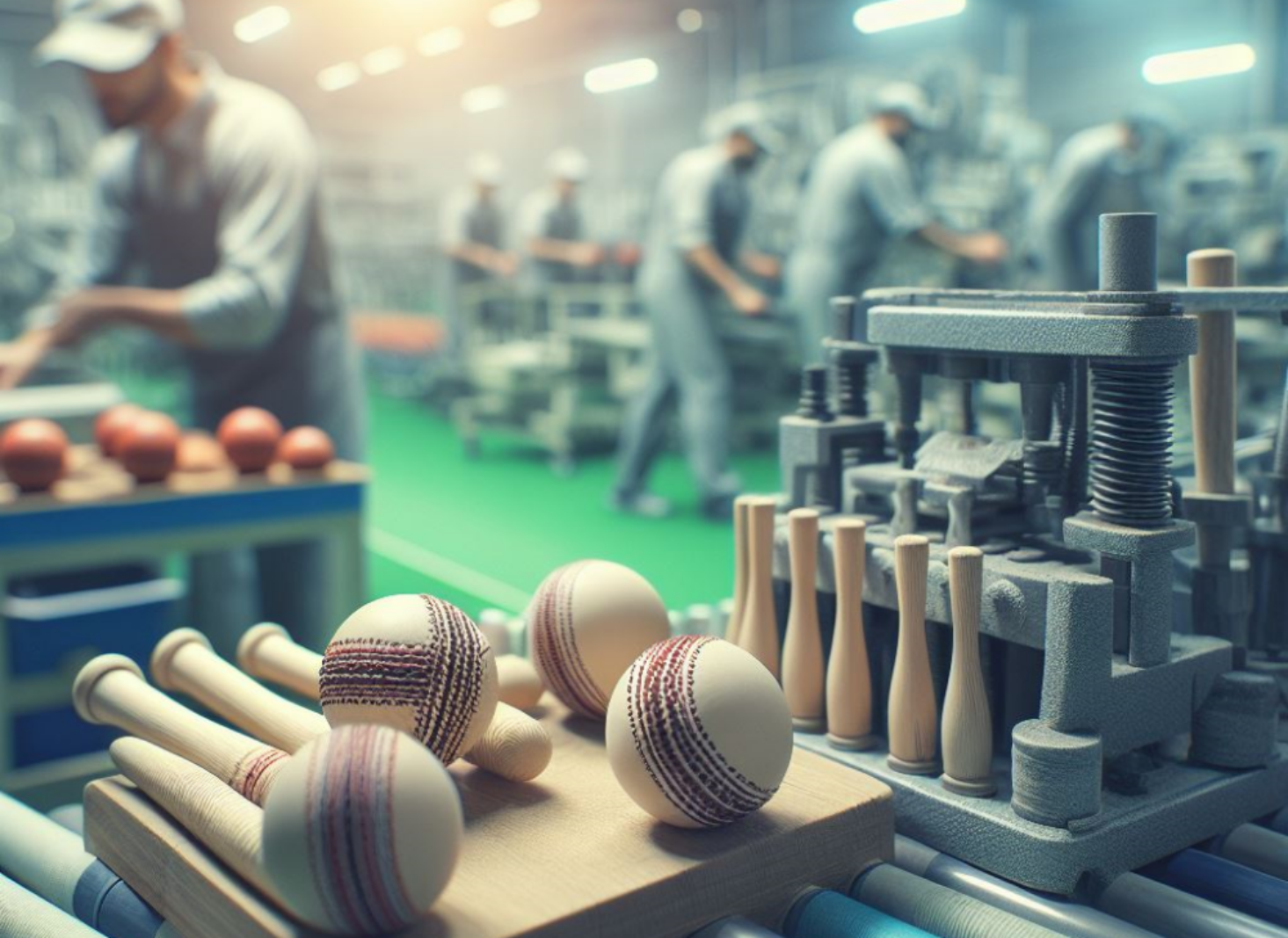
How Are Cricket Balls Manufactured
The world of cricket is a captivating blend of skill, strategy, and precision, and at its core lies one of the most fundamental elements—the cricket ball. Delving into the intriguing process of how cricket balls are manufactured unveils a journey of craftsmanship and technicality that shapes the very essence of the game.
The artistry of crafting cricket balls begins with meticulous attention to detail in selecting the finest materials. From the core to the outer layers, every component contributes to the ball’s performance on the pitch.
As we explore the fascinating world of cricket ball manufacturing, the nuances of material selection come to light, showcasing the significance of quality in the creation of this essential cricketing gear.
The manufacturing process is a symphony of engineering precision and traditional craftsmanship. The inner core, often made of cork, serves as the nucleus, providing the ball with its essential bounce and resilience.
Layers of meticulously cut leather are then carefully stitched to encapsulate the core, a process that demands skill and precision. This journey into the heart of cricket ball production reflects the fusion of technology and tradition, where each stitch contributes to the ball’s aerodynamics and durability.
Crucial to the understanding of cricket ball manufacturing is the role it plays in the game’s dynamics. The quality and construction of the ball can significantly impact its behavior—swinging, seaming, or spinning.
A deep dive into the intricacies of this process sheds light on how variations in manufacturing can influence the trajectory of a match.
In the realm of cricket equipment, the cricket ball holds a unique position, symbolizing the very essence of the sport. The process of its creation mirrors the commitment to excellence that defines the game.
Join us on this exploration of how cricket balls are manufactured, where each phase of production contributes to the legacy of cricketing tradition and the pursuit of perfection on the field.
The Manufacturing Process of Cricket Balls
Curious about how cricket balls are made? Delve into the fascinating world of cricket ball manufacturing! Discover the materials used, the intricacies of inner core construction, the art of outer shell construction, and the meticulous process of stitching the seams.
Get ready to uncover the secrets behind these essential components of the iconic cricket ball.
Materials Used in Cricket Ball Manufacturing
Cricket balls are made using a combination of materials to ensure durability, performance, and safety during the game. The materials used in cricket ball manufacturing, including Cork and rubber for the core, leather for the shell, and waxed cotton for the thread, vary depending on the type of ball and playing conditions.
Here is a breakdown of the materials commonly used:
1. Core: Cork and rubber 2. Shell: Leather 3. Thread: Waxed cotton 4. Seam: Stitched with a strong, thick thread
Each material plays a crucial role in the ball’s performance and durability. The cork and rubber core provides the ball’s bounce, while the leather shell adds durability and grip. Waxed cotton thread ensures the seam stays intact even after intense use.
These materials, used in cricket ball manufacturing, combine to create a cricket ball that meets the requirements of the game and provides an optimal playing experience.
Inner Core Construction
The inner core construction of a cricket ball is an important aspect that determines its performance. It consists of layers of tightly wound strings, typically made from cork and rubber, which are shaped into a spherical core. These layers are wrapped around a cork nucleus to give the ball its weight and bounce.
The materials used in the inner core construction, namely the cork and rubber layers, determine the ball’s durability and resilience.
The number of layers and the quality of the materials used in the inner core construction affect the ball’s weight, bounce, and durability.
Additionally, the inner core construction plays a crucial role in maintaining the ball’s spherical shape and ensuring consistent performance throughout a match.
Outer Shell Construction
The process of manufacturing cricket balls begins with the crucial step of outer shell construction. In order to create the outer shell, high-quality leather, such as cowhide, is carefully selected for its durability and performance.
To achieve the desired shape, circular pieces of leather are cut using a die cutter. After the cutting process, the edges of the leather pieces are meticulously trimmed and sanded to ensure uniformity and smoothness.
For added strength and durability, multiple layers of leather are then stacked and effectively glued together to form the outer shell.
Next, the stacked leather layers are placed in a mold and compressed using heavy machinery to achieve the desired shape.
Once the molding process is complete, the molded shell is carefully removed from the mold and hand-stitched using a nylon or polyester thread.
To give the cricket ball a polished and professional look, the stitched shell is stamped with brand logos and meticulously polished, resulting in a smooth texture.
To continuously improve the durability and performance of cricket balls, manufacturers are constantly exploring new materials and designs for the outer shell construction. Suggestions for enhancement include utilizing synthetic materials to enhance water resistance and developing advanced stitching techniques to increase strength and longevity.
Stitching the Seams
When it comes to stitching the seams of cricket balls, there are specific techniques and considerations involved. Here is a list of key points to understand:
- The stitching of cricket ball seams is crucial for its performance. The seam is traditionally hand-stitched using waxed linen thread.
- Two parallel stitches: The seam is created by stitching two parallel rows of stitching on either side of the seam. This helps to maintain the ball’s shape and aerodynamics.
- Tight and even stitching: The stitches must be tight and evenly spaced to ensure the seam remains intact during the game. This is essential for accurate bowling and swing.
- Seam thickness: The thickness of the seam is an important factor. It should be substantial enough to provide grip for the bowler but not too thick that it affects the ball’s balance or bounce.
- Seam orientation: The way the seam is positioned on the ball affects its movement in the air. The bowler strategically aligns the seam to generate swing or seam movement.
When it comes to stitching the seams of cricket balls, there are specific techniques and considerations involved. Here is a list of key points to understand:
- The stitching of cricket ball seams is crucial for its performance. The seam is traditionally hand-stitched using waxed linen thread.
- Two parallel stitches: The seam is created by stitching two parallel rows of stitching on either side of the seam. This helps to maintain the ball’s shape and aerodynamics.
- Tight and even stitching: The stitches must be tight and evenly spaced to ensure the seam remains intact during the game. This is essential for accurate bowling and swing.
- Seam thickness: The thickness of the seam is an important factor. It should be substantial enough to provide grip for the bowler but not too thick that it affects the ball’s balance or bounce.
- Seam orientation: The way the seam is positioned on the ball affects its movement in the air. The bowler strategically aligns the seam to generate swing or seam movement.
Quality Control in Cricket Ball Manufacturing
In the world of cricket ball manufacturing, one crucial aspect that ensures top-notch quality is the meticulous process of quality control.
In this section, we delve into the importance of maintaining precise weight and dimensions, the role of hardness and bounce, and the crucial aspect of seam alignment.
Join us as we uncover the secrets behind crafting cricket balls that meet the highest standards of performance, ensuring an exhilarating game for players and spectators alike.
Weight and Dimensions
1. Red Leather Balls (Traditional)
- 155.9 to 163.0 grams
- Circumference: 22.4 to 22.9 centimeters
- Diameter: 7.0 to 7.2 centimeters
2. White Balls (Limited-Overs)
- 156.0 to 163.0 grams
- Circumference: 22.4 to 22.9 centimeters
- Diameter: 7.0 to 7.2 centimeters
3. Pink Balls (Day-Night Test Matches)
- 156.0 to 163.0 grams
- Circumference: 22.4 to 22.9 centimeters
- Diameter: 7.0 to 7.2 centimeters
To ensure fair play and consistency, it is essential for manufacturers to adhere to these weight and dimension guidelines. Any variations beyond the specified ranges may lead to the ball being deemed unfit for use. Maintaining consistent weight and dimensions across batches is crucial for maintaining the integrity of the game.
The weight and dimensions of cricket balls play a vital role in their performance and conformity to regulations. Manufacturers must carefully craft cricket balls that meet these weight and dimension specifications to ensure a fair and enjoyable game.
Hardness and Bounce
The hardness and bounce of a cricket ball are crucial factors in its performance on the field. When choosing a cricket ball, consider the following:
- Hardness: Look for a ball with the right level of hardness. A ball that is too hard may not grip the pitch effectively, while a ball that is too soft may not provide enough bounce.
- Bounce: Consider the bounce of the ball. A ball that bounces too much may make it easier for the batsman to play shots, while a ball with inconsistent bounce can make it challenging for the batsman to anticipate the ball’s movement.
In a memorable match, the hardness and perfect bounce of the cricket ball helped the bowler take a stunning wicket, leading their team to victory. The ball’s characteristics played a significant role in creating an exciting and competitive game.
Seam Alignment
Proper seam alignment is crucial in the manufacturing of cricket balls as it affects the ball’s trajectory and movement during gameplay. Here is a table illustrating the importance of seam alignment in cricket ball manufacturing:
1. Seam Position: Affects the swing and spin of the ball. A well-aligned seam allows for more controlled movement in the air and off the pitch. 2. Seam Height: Influences bounce and unpredictability. A consistent seam height ensures fair play and challenges the batsman. 3. Seam Firmness: Impacts grip and control for bowlers. An aligned and firm seam helps bowlers achieve desired seam movement and variation.
Properly aligned seams enhance the overall performance and quality of cricket balls, providing an exciting and challenging experience for both bowlers and batsmen.
The Evolution of Cricket Balls
Cricket balls have undergone a remarkable evolution over the years, catering to the distinctive demands of the game’s various formats.
From the traditional red leather balls to the use of white balls in limited-overs cricket, and the introduction of pink balls for day-night Test matches, each sub-section in this exploration will shed light on the fascinating journey and unique characteristics of these cricketing essentials.
Get ready to uncover the secrets behind the manufacturing and significance of cricket balls throughout history.
Traditional Red Leather Balls
Traditional red leather balls have been an integral part of cricket for decades. Here are some key points to consider about these iconic cricket balls:
- Material: Traditional red leather balls are made from high-quality cowhide leather, carefully selected for durability and performance.
- Construction: The inner core of the ball consists of layers of cork, tightly wound with string. The outer shell is made of leather, which is stitched together to give the ball its distinctive shape.
- Characteristics: Red leather balls are known for their swing and seam movement. The leather outer surface provides grip to the bowlers, allowing them to generate movement in the air and off the pitch.
- Usage: Red leather balls are used in Test matches and first-class cricket. They are preferred for their durability and ability to hold up well over extended periods of play.
In a true story, during the Ashes series in 1981, England’s Ian Botham produced a remarkable performance with traditional red leather balls. He single-handedly turned the game in England’s favor with a stunning all-round display, helping his team win against Australia.
White Balls for Limited-Overs Cricket
The use of white balls in limited-overs cricket matches is specifically designed to enhance various aspects of the game. When it comes to white balls, there are some key points worth mentioning:
- Enhanced Visibility: The white color of the ball significantly improves visibility for players, spectators, and television viewers alike.
- Unmatched Durability: White balls are crafted using high-quality materials that ensure their durability and enable them to withstand the rigors of limited-overs cricket.
- Distinct Contrast: The white color of the balls provides a noticeable contrast against the colored clothing worn by players, making it much easier to spot the ball during gameplay.
- Perfect for Night Matches: In day-night matches, where visibility becomes crucial under floodlights, white balls prove to be particularly useful.
Fun Fact: It was in 1979 that Australia and West Indies played the first limited-overs cricket match using a white ball. This marked the beginning of a new era in cricket.
So, it is clear that white balls play a crucial role in limited-overs cricket, offering improved visibility, durability, contrast, and suitability for night matches.
Pink Balls for Day-Night Test Matches
Pink balls for day-night test matches have become a crucial component in cricket. These balls, specifically designed for better visibility under floodlights, are a game-changer. The pink color not only helps players but also allows spectators to see the ball more clearly during evening sessions.
The introduction of pink balls has brought an exciting dimension to the game, enabling test matches to be played during twilight hours. Players and fans alike have embraced this innovation, as it creates a unique atmosphere and challenges players in different lighting conditions.
The use of pink balls in day-night test matches has now become an integral part of cricket ball manufacturing’s future.
The concept of using pink balls in cricket dates back to the mid-2000s when Kookaburra, a cricket equipment company, conducted extensive research and development.
Their aim was to create a ball that would be more visible in floodlit conditions. With various trials and modifications, pink balls were successfully introduced in domestic day-night matches and eventually made their way into international test cricket.
This implementation of pink balls has revolutionized the way test matches are played. It provides a thrilling spectacle for players and spectators alike.
The Future of Cricket Ball Manufacturing
The future of cricket ball manufacturing is being shaped by advancements in technology and materials. Here are some exciting potential developments to anticipate:
- Smart cricket balls: With sensors embedded in the ball, real-time data on speed, spin, and trajectory can be provided.
- Eco-friendly materials: Manufacturers may adopt sustainable materials that not only reduce environmental impact but also maintain performance.
- Customizable balls: Players can have the choice to personalize the weight, bounce, and grip of the ball according to their playing style.
- Improved durability: By implementing innovations in materials and construction, cricket balls can become more resistant to wear and tear, thus extending their lifespan.
Frequently Asked Questions
How are cricket balls manufactured?
Cricket balls are manufactured through a multi-stage process that involves various materials and precision. The manufacturing process remains relatively similar regardless of the manufacturer.
What is involved in stage 1 of the manufacturing process?
In stage 1, the inner core of the cricket ball is created using cork, typically sourced from the Portuguese Cork Oak tree. The cork is ground down and compressed into a small round ball.
What happens in stage 2 of the manufacturing process?
During stage 2, the inner core is sandwiched between two slices of cork or leather, which gives the ball its density and shape. This forms the outer core of the cricket ball.
How is the outer covering of the cricket ball made?
The outer casing of the cricket ball is made from high-quality leather, usually obtained from cows. The leather is dyed, cut to shape, and then stitched together to create perfect hemispheres.
What is the significance of the raised seam on a cricket ball?
The four pieces of leather that make up the cricket ball are stitched together with string to form a raised seam. The raised seam plays a crucial role in determining the ball’s trajectory and enables bowlers to achieve variations in swing and spin.
What are the quality control measures for cricket ball manufacturing?
Cricket balls undergo quality control checks to ensure they meet universal guidelines. These checks include verifying the weight, circumference, bounceability, and spherical shape of the ball. The manufacturer’s name is also stamped or pressed onto the ball.
Are there different types of cricket balls?
Yes, there are different types of cricket balls. In addition to the traditional red balls, white and pink balls have been introduced for specific formats of the game. Each type of ball may have slight variations in their manufacturing processes to meet the specific playing requirements.